在目前广泛应用于数控车床、纺织机械等领域的伺服系统中,采用全数字的控制方式已是大势所趋。数字化控制与模拟控制相比不仅具有控制方便、性能稳定、成本低廉等优点,同时也为伺服系统实现网络化、智能化控制开辟了发展空间。全数字控制的伺服系统不仅可以方便的实现电机控制,同时通过软件的编程可以实现多种附加功能,使得伺服系统更为人性化,智能化,这也正是模拟控制所不能达到的。 目前,对伺服系统的研究已有大量的文献[1-5]进行了报道。本文基于ti公司f2407a dsp控制芯片,建立了全数字控制的伺服系统thrsv-1,该系统可以工作于定位、脉冲跟踪、模拟量跟踪、力矩给定、调速五种模式。在采用1024脉冲/转的光电编码盘时,电机的定位精度可以达到每转的1/4096。当工作于脉冲跟踪模式时,其转速随着脉冲频率的变化而改变,转过的角度和输入脉冲的总数成正比。而在模拟量跟踪时可以实现s曲线、阶跃、正弦等多种速度曲线,真正实现任意速度曲线的跟踪。力矩模式使得电机输出力矩恒定,可用于多台联动的场合。最后,基本的调速方式满足最为常用的控制要求,当电机工作于额定转速以上时,采用了弱磁升速技术。
磁场定向控制原理 为了分析方便,先对三相异步电机做如下理想化假定: 电机定转子三相绕组完全对称; 定转子表面光滑,无齿槽效应,定转子每相气隙磁动势在空间呈正弦分布; 磁饱和、涡流及铁心损耗忽略不计。 [align=center]
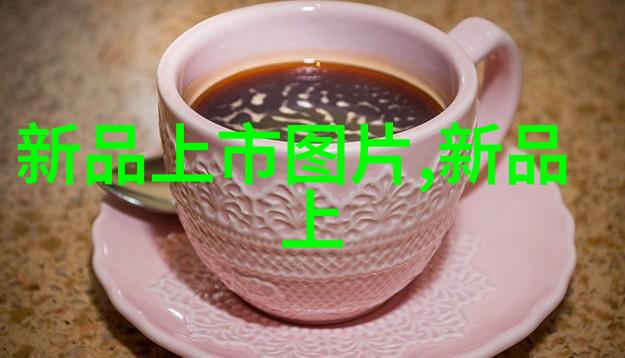
图1异步电机α—β和d—q坐标系[/align] 图1是三相异步电机的坐标图,其中a、b、c分别为三相定子绕组,α-β为两相定子坐标,d-q为两相以ωo角速度旋转的坐标,isd、isq、isα、isβ分别是定子电流矢量is在d、q、α、β轴上的分量。 对于一般电机调速系统而言,从转矩到转速近似为一个积分环节,其积分时间常数由电机和负载的机械惯量决定,为不可控量,因此转矩控制性能的好坏直接关系到一个调速系统的动静态特性。从转矩表达式可以看出,异步电机的转矩一般和定子电流矢量和转子磁场以及夹角有关。因此,要想控制转矩,必须先检测和控制磁通。在磁场定向矢量控制中,一般把d-q坐标系放在同步旋转磁场上,把静止坐标系中的各交流量转化为旋转坐标系中的直流量,并使d轴和转子磁场方向重合,此时转子磁通q轴分量为零(ψrg=0),此时有如下几式:
其中式(1)-(5)为转子磁场定向控制方程式。漏磁系数=1-lm2/lslr,τr=lr/rr为转子时间常数,ωs为转差角速度,ω0转子旋转磁场的角速度,ωr是转子旋转角速度。式(3)-(6)是转子磁场定向控制的电流模型公式,用来计算转子旋转磁场的幅值和角度。由式(3)不难发现,只需检测定子电流的d轴分量即可观测出转子磁通幅值。由式(7)可知,当ψrd恒定时,电磁转矩和电流的q轴分量或转差成正比,没有最大值限制,通过控制定子电流的q轴分量即可控制电磁转矩。因此,也称定子电流的d轴分量为励磁分量,定子电流的q轴分量为转矩分量。因此,可以通过定子电流的d轴分量控制转子磁通,q轴分量来控制转矩,从而实现了磁通和转矩的解耦控制。 [align=center]
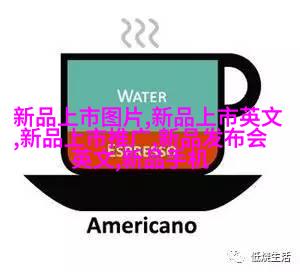
图2伺服系统模型[/align] 图2是整个转子磁场定向控制的原理框图,整个系统由三个环组成,由外到内分别是位置环、速度环、电流环。其中位置环是在采用定位模式时进行闭环控制,在其他工作模式下不进行电机轴位置量的控制。
系统软硬件设计 硬件设计 dsp以及周边资源 以dsp为核心的伺服系统硬件如图4,整个系统的控制电路由dsp+gal组成。 其中gal主要用于系统io空间的选通信号以及开关驱动信号的输出控制等。dsp作为控制核心,接受外部信息后判断伺服系统的工作模式,并转换成逆变器的开关信号输出,该信号经隔离电路后直接驱动ipm模块给电机供电。另外eeprom用于参数的保存和用户信息的存储。功率电路 整个主电路先经不控整流,后经全桥逆输出。逆变器选用igbt智能模块。该模块采用10a,600v的功率管,内部集成了驱动电路,并设计有过电压、过电流、过热、欠电压、等故障检测保护电路。系统的辅助电源采用线性稳压电源,主要供电包括六路开关管的驱动电源,dsp和gal以及i/o口控制芯片的电源和采样lem以及光电编码器的电源。电流采样电路 本系统的设计要求至少采样两相电流,由于负载的对称性,故采样ia和ic两相电流。采样电路采用霍尔传感器并经模拟电路处理在3.3v的电压范围内,然后送入dsp的ad转换器中。 转子位置检测电路 电机反馈采用增量式光电编码器,该编码器分辨率为1024脉冲/转,输出信号包括a、b、z脉冲信号,其中a、b信号互差90o(电角度),dsp通过判断a、b的相位和个数可以得到电机的转向和速度。z信号每转一圈出现一次,用于位置信号的复位。光电编码盘脉冲信号送入dsp后,经内部qep电路实现四倍频,因此电机每圈的脉冲数是4096个。保护电路 系统在主回路设置了过压、欠压、igbt故障、电机过热、编码器故障,故障信号经逻辑电路后可直接封锁开关脉冲,同时通过dsp的i/o口输入,通过软件检测来实现系统的保护。 软件设计 dsp伺服控制程序由3个部分组成:主程序的初始化、pwm定时中断程序和dsp与周边资源的数据交换程序。 主程序 主程序先完成系统的初始化、i/o口控制信号管理、dsp内各个控制模块寄存器的设置等,然后进入循环程序,在这里完成系统的数据保存和报警内容的更新。 pwm定时中断程序 pwm定时中断程序是整个伺服控制程序的核心内容,在这里实现电流环、速度环、位置环的采样控制以及矢量控制、pwm信号生成、各种工作模式选择和i/o的循环扫描。中断控制程序周期为50μs,即ipm开关频率为20khz。其中每个周期完成电流环的采样和开关信号的输出,每10个开关周期完成一次速度环和位置环控制。pwm控制信号采用svpwm调制方法生成,在每个采样周期中对每相电流进行一次pid算法来决定该周期中的占空比。 数据交换程序 数据交换程序主要包括与上位机的通讯程序、eeprom中参数的存储、键盘值的读取和数码管显示程序。其中通讯采用rs232接口,根据特定的通讯协议接受上位机的指令,并根据要求传送参数。eeprom的数据交换通过dsp的spi口完成。键盘和数码管显示在每隔1200个周期扫描一次,更新显示和键值。 [align=center]

图3伺服系统硬件构成
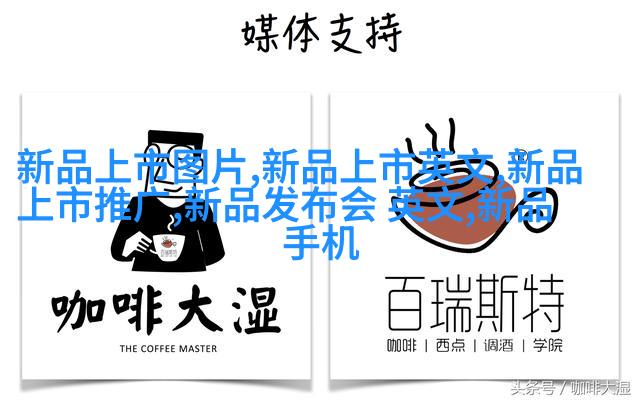
图4dsp系统硬件图[/align]
实验结果 [align=center]

图5伺服系统速度阶跃响应曲线

图6速度给定反相时的相电流波形

图7伺服定位时的位置波形

图8电机在1200r/min时的磁链圆[/align] 上述伺服系统采用三相异步电动机:额定功率180w,额定电流0.65a,额定转速1400r/min,额定转矩1.1nm,定子电感42mh,定子电阻28ω。电流环采样周期50μs,速度环采样周期500μs,位置环采样周期500μs。图5是速度阶跃响应曲线,通过调整速度环pid参数可以改变速度波形的超调量和响应时间。图6是转速正反切换时的相电流波形,可以清楚的看到当电机转向发生变化时,其相电流波形反相。图7是伺服系统在定位2圈时的位置波形,该电机位置由光码盘决定,即每采集到4096个脉冲为一圈。图8是伺服系统在1200r/min时的转子磁链圆轨迹。
结语 本文中,系统硬件上采用dsp加gal的控制结构,电路设计简单,紧凑,满足了矢量控制实时性的要求,同时全数字化的控制,使系统在控制精度、功能和抗干扰能力上都有了很大程度的提高。同时,由f2407a控制的全数字伺服系统通过软件编程,可以实现定位、模拟量、力矩给定等多种工作方式,且工作性能稳定。实验结果表明,本文的伺服系统在完成定位、调速时具有很高的控制精度,不仅满足高性能定位系统的应用要求,而且也可用于伺服系统的教学中。
作者简介 蒋中明(1976-) 男 浙江天煌科技实业有限公司工程师,主要从事电气传动控制及dsp控制技术产品的研究与开发。